PU Pumps for Casting
In casting operations, Polyurethane (PU) pumps are frequently utilized to handle and dispense polyurethane ingredients. These pumps are made to deal with the unique characteristics of polyurethane, including its abrasiveness, viscosity, and reactivity.
Key Features of PU Pumps for Casting :
- Materials like stainless steel or specialty coatings are used to make components that are resistant to the abrasiveness and chemicals of polyurethane.
- To guarantee constant casting quality, precise metering and flow rate control are necessary.
- High Pressure Capability : Able to handle the pressures up to 20 kv required for injecting polyurethane into molds.
The capacity to withstand the pressures necessary for injecting polyurethane into molds is known as high pressure capability. - Easy Maintenance : Designed for easy disassembly and cleaning to minimize downtime.
To save downtime, components are designed for simple removal and cleaning. - Durability : Built to withstand the harsh conditions of polyurethane processing.
Made to resist the demanding circumstances involved in the production of polyurethane.

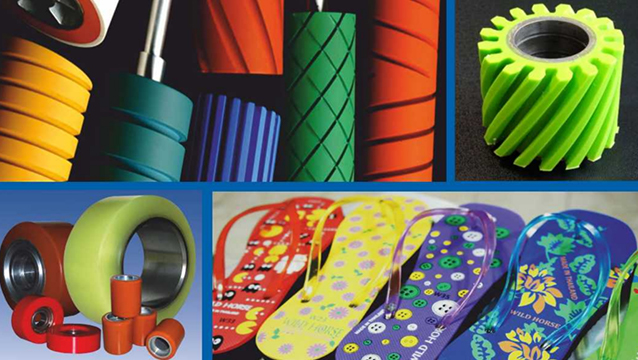
Benefits of PU Pumps for Casting :
In summary, PU pumps offer a range of benefits for casting applications, including durability, chemical resistance, versatility, efficiency, low maintenance, cost-effectiveness, design flexibility, and safety. These advantages make them a preferred choice for many casting operations.
Polyurethane (PU) pumps are widely used in casting applications due to their numerous benefits. Here are some of the key advantages:
- Durability and Wear Resistance :
- High Durability : PU pumps are highly durable and resistant to wear and tear. This makes them ideal for handling abrasive materials commonly used in casting processes.
- Longer Lifespan : Due to their wear resistance, PU pumps typically have a longer operational lifespan compared to other types of pumps.
- Chemical Resistance :
- Resistance to Chemicals : PU pumps are resistant to a wide range of chemicals, including solvents, oils, and fuels. This chemical resistance makes them suitable for various casting applications where chemical exposure is common.
- Versatility :
- Broad Range of Applications : PU pumps can handle a variety of materials, including slurries, resins, and other casting compounds. This versatility allows them to be used in different stages of the casting process.
- Customizability : PU pumps can be customized to meet specific requirements of the casting process, including different sizes, shapes, and material properties.
- Efficiency :
- High Efficiency : PU pumps often operate at high efficiency, ensuring that materials are transported with minimal energy consumption. This efficiency can lead to cost savings in energy usage.
- Consistent Performance : They provide consistent performance, which is crucial for maintaining the quality and precision of casting operations.
- Maintenance and Cost-Effectiveness :
- Low Maintenance : PU pumps require relatively low maintenance due to their durability and resistance to wear and chemicals. This reduces downtime and maintenance costs.
- Cost-Effective : Over time, the longevity and low maintenance requirements of PU pumps make them a cost-effective choice for casting operations.
- Flexibility in Design :
- Adaptable Design : PU pumps can be designed to fit various casting systems and can be easily integrated into existing setups. This flexibility makes them a convenient choice for upgrading or expanding casting operations.
- Lightweight : They are often lighter than metal pumps, making them easier to handle and install.
- Safety and Environmental Benefits :
- Non-Toxic : Polyurethane is generally non-toxic, making PU pumps safer for workers and the environment.
- Environmentally Friendly : They can be designed to minimize waste and are often more environmentally friendly compared to metal pumps, which may corrode and require more frequent replacements.
PU Pumps for Casting application industries :
Peristaltic (PU) pumps are widely used in casting application industries due to their ability to handle abrasive, viscous, and shear-sensitive fluids. Here are some key points about their application in these industries :
- Handling Abrasive Materials : PU pumps are designed to handle abrasive slurries and fluids, making them ideal for moving materials like sand, clay, and other casting media.
- Gentle Pumping Action : The gentle peristaltic action minimizes shear, preventing damage to delicate materials and maintaining the integrity of the mix.
- Precision Dosing: Thes e pumps offer precise control over flow rates, which is crucial for ensuring consistent and accurate mixing ratios in casting processes.
- Chemical Compatibility : PU pumps are resistant to a wide range of chemicals, allowing them to handle various additives and cleaning agents used in casting processes.
- Self-Priming and Dry Running : They can self-prime and run dry without damage, providing flexibility in operations and reducing maintenance needs.
- Low Maintenance : With no valves, seals, or glands, PU pumps require less maintenance compared to other types of pumps, reducing downtime and operational costs.
Benefits of PU Pumps in Casting Applications :
Applications in Casting Industries :
When selecting a PU pump for casting, consider the following factors :
- Mold Making : PU pumps are used to transfer and mix materials for mold making, ensuring a consistent and homogenous mixture.
- Slurry Transfer : These pumps handle the transfer of ceramic slurries, investment casting materials, and other thick, abrasive fluids involved in casting processes.
- Additive Dispensing : PU pumps are utilized for precise dosing of additives, hardeners, and binders required in various casting formulations.
- Cleaning and Flushing : Due to their chemical resistance, PU pumps are suitable for flushing and cleaning equipment, ensuring that systems remain free from residual materials that could affect product quality.
- Material Recycling : In processes where materials are recycled or reused, PU pumps efficiently transfer and process these materials, maintaining the quality and consistency required for subsequent casting operations.
Considerations while selecting PU pump for Casting :
Choosing the right PU pump for a casting process involves understanding the specific requirements of the material and the application. Proper selection and maintenance of the pump are crucial for efficient and high-quality production. Overall, PU pumps provide a versatile and reliable solution for various applications within the casting industry, contributing to improved efficiency, reduced downtime, and higher quality products.
- Material Compatibility : Ensure the pump tubing and materials are compatible with the specific chemicals and abrasives used in the casting process.
- Flow Rate and Pressure Requirements : Select a pump that meets the necessary flow rate and pressure for the application to ensure efficient operation.
- Chemical Compatibility : Ensuring all wetted parts of the pump are compatible with the polyurethane formulation.